AGV servo motor
AGV is characterized by wheeled movement. Compared with walking, crawling or other non-wheeled mobile robots, AGV has the advantages of fast action, high work efficiency, simple structure, strong controllability, and good safety. Traditional AGV uses electromagnetic guidance, tape guidance, optical guidance, and other methods to set up its travel route. The path is single and suitable for fixed operation processes, which cannot meet the needs of modern logistics systems.
AGV is characterized by wheeled movement. Compared with walking, crawling or other non-wheeled mobile robots, AGV has the advantages of fast action, high work efficiency, simple structure, strong controllability, and good safety. Traditional AGV uses electromagnetic guidance, tape guidance, optical guidance, and other methods to set up its travel route. The path is single and suitable for fixed operation processes, which cannot meet the needs of modern logistics systems.
In China, with the rapid development of the logistics system, the application scope of AGV is also expanding. How to develop AGV system technology that can meet all aspects of users' needs (function, price, and quality) is a practical problem we must face in the future. Fully automatic AGV technology, which pursues the automation of AGV, almost does not need manual intervention, and the path planning and production process are complex and changeable. It can be used in almost all handling occasions, especially in the intelligent warehousing and logistics industry. In order to pursue the optimal path, the adjustment system usually needs to produce different path planning, and the traditional fixed path guidance method cannot be used. Inertial guidance combined with high-precision drive and steering systems can meet the needs of changeable paths.
By improving the rotor pole structure and selecting the encoder with a memory structure, the closed-loop of current, speed, and position is realized, so as to achieve small torque fluctuation and accurate positioning.
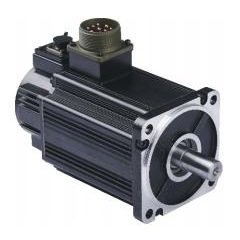
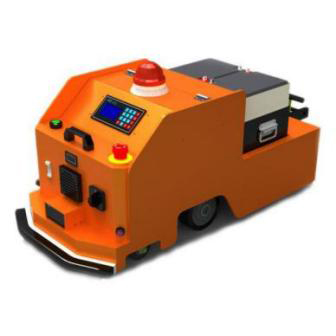